The Big Guide to Hydrogen
Hydrogen is important because it is a critical ingredient in most green fuels.
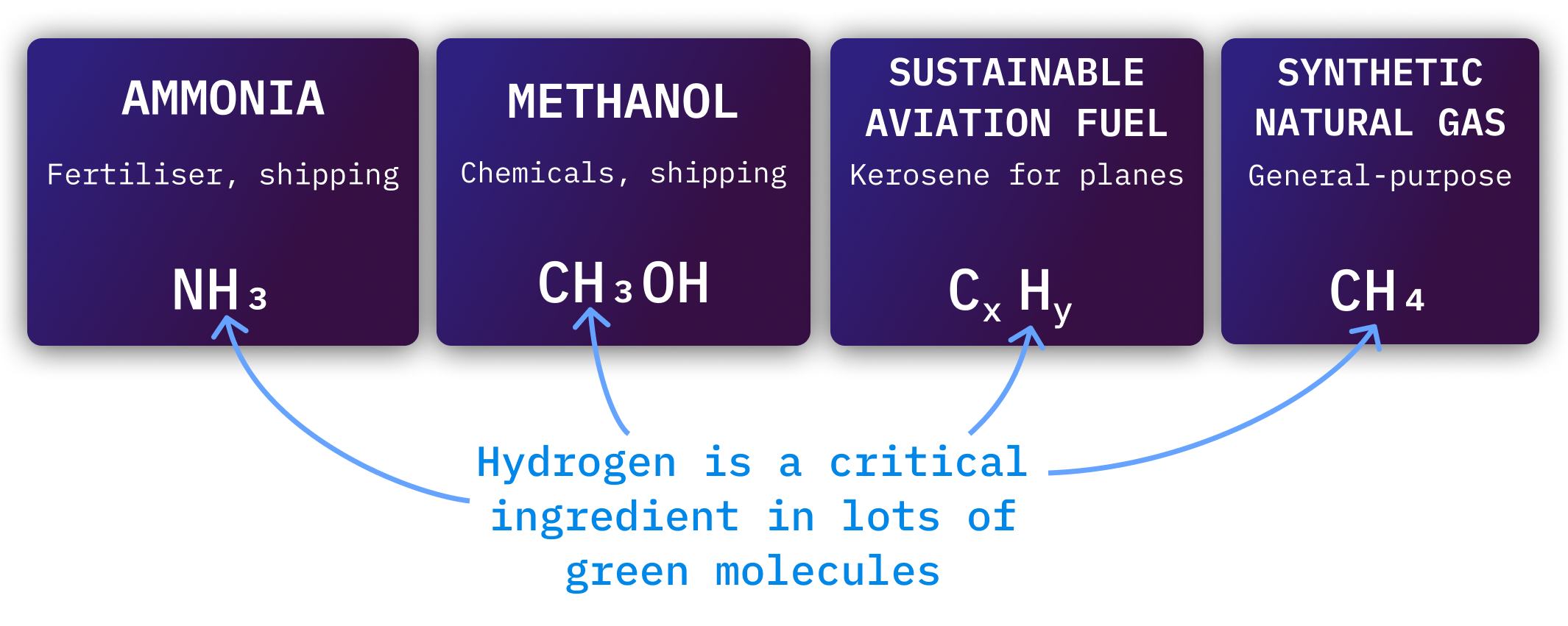
Hydrogen is also the dominant cost in other clean fuels. It is not possible to produce cheap green ammonia or Sustainable Aviation Fuel without cheap hydrogen.
Steel, shipping, aviation, and chemicals will need a lot of hydrogen to decarbonise. In most cases, they won’t use hydrogen directly, but will use chemicals built from hydrogen.
Caution! Sometimes hydrogen is shit!
Often, using electricity instead of hydrogen is cheaper and safer.
Here’s an example: we could use hydrogen for cars, but we don’t. EVs eat hydrogen cars for breakfast.
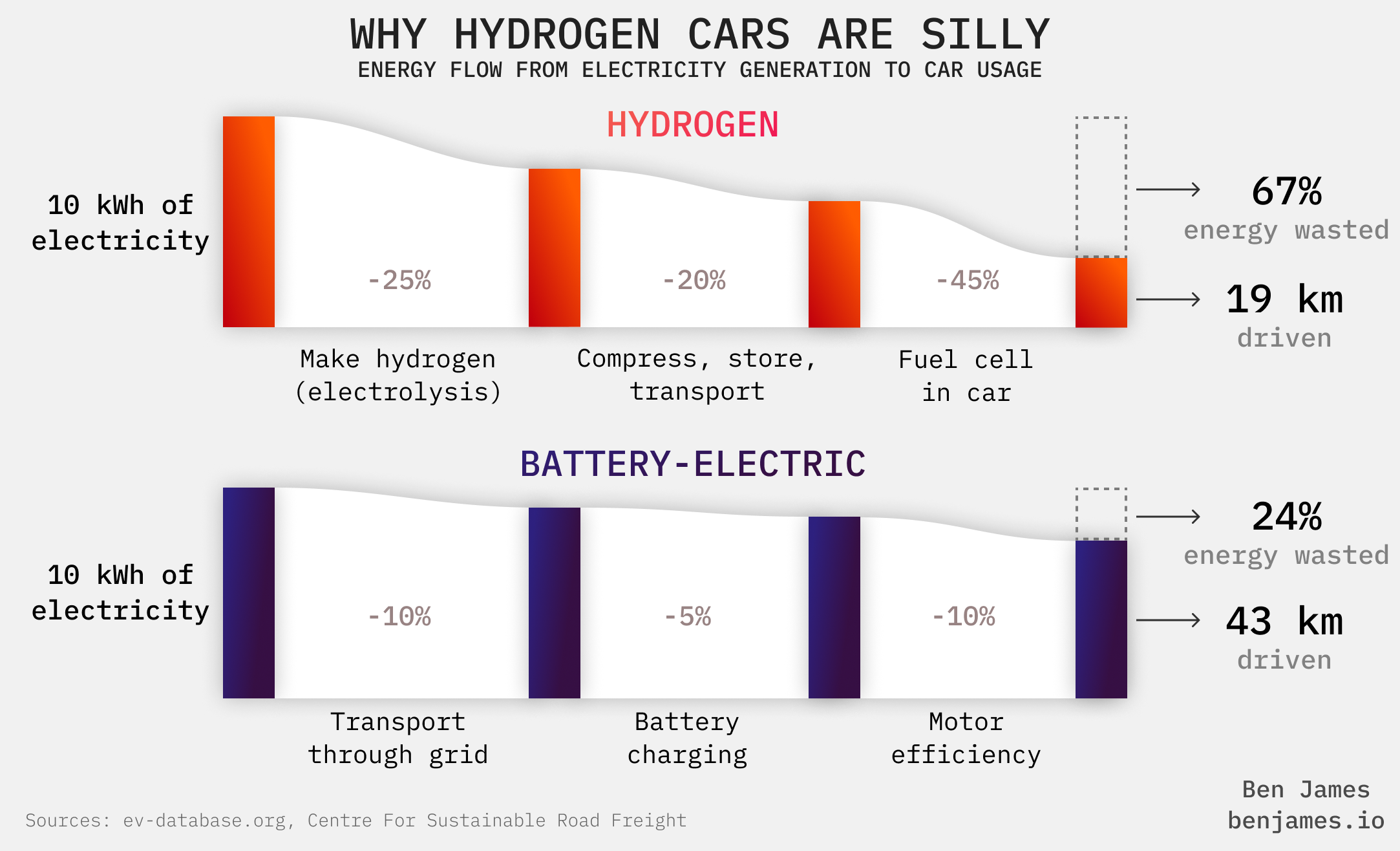
Here’s a simple guide to where we should use hydrogen to decarbonise.
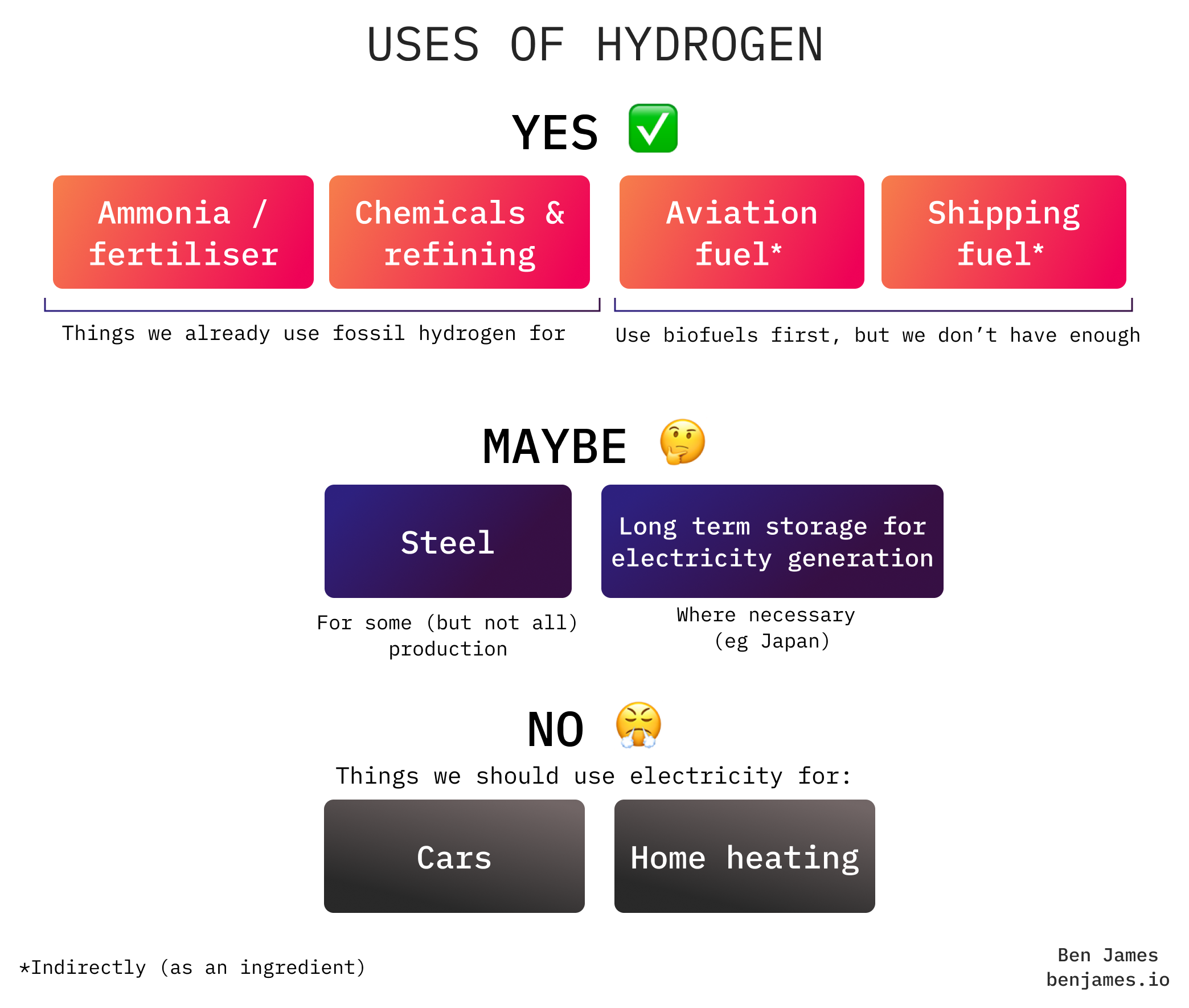
For a more detailed version, check out Michael Liebreich’s hydrogen ladder. He does an excellent 20 minute walkthrough.
Now let’s get into the interesting bit. How do we produce hydrogen?
Making hydrogen
Today, hydrogen is a climate problem, not a solution.
We already make a lot of hydrogen today - about 100 million tons a year. It’s mainly used to:
- Make ammonia for fertiliser, and
- Refine oil and produce petrochemicals.
This means that producing hydrogen is responsible for 2% of total emissions, and 6% of global natural gas usage.
Today, we mostly make hydrogen with a process called Steam Methane Reforming (SMR). We call this type of hydrogen grey hydrogen, because it uses fossil fuels.
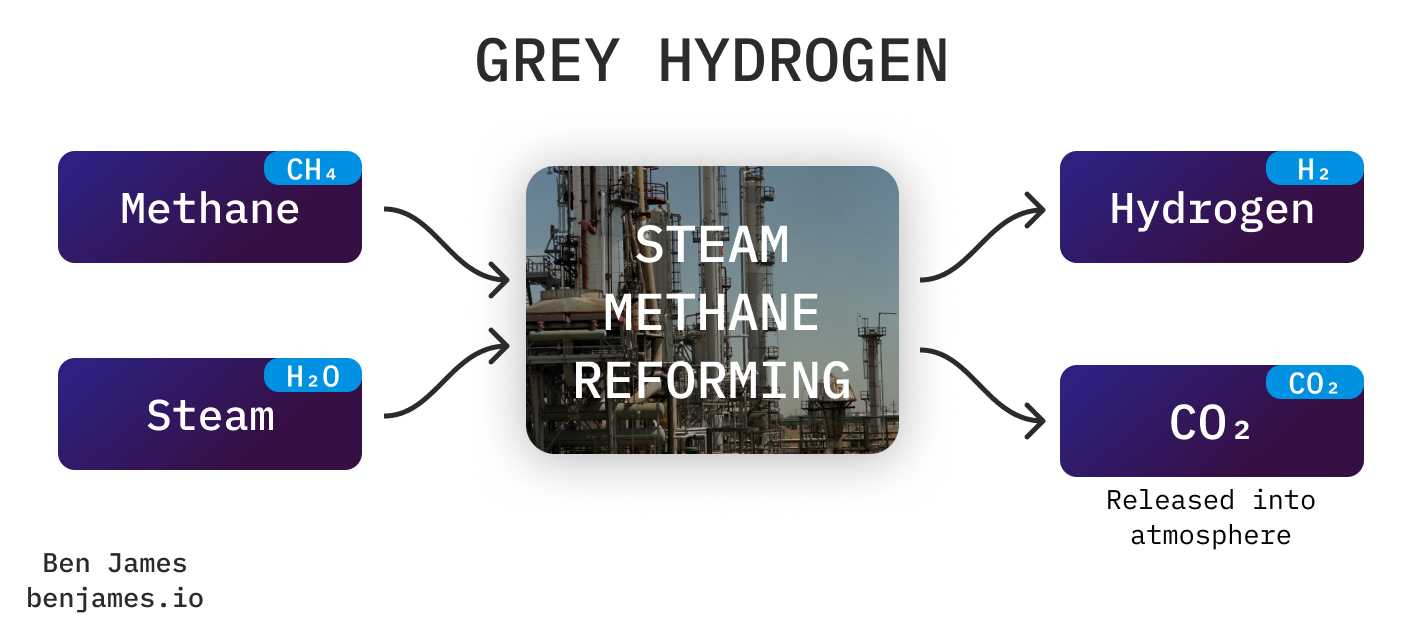
About 70% of global hydrogen is made using methane (natural gas). In China, coal is often used, which emits about 2x the CO2. China is coal-rich and gas-poor, so it's a logical choice.
Clean hydrogen
Fossil fuels are cringe, so we need find a way to produce hydrogen cleanly. There are two main methods.
Blue hydrogen
Blue hydrogen simply takes grey hydrogen and slaps carbon capture on top.
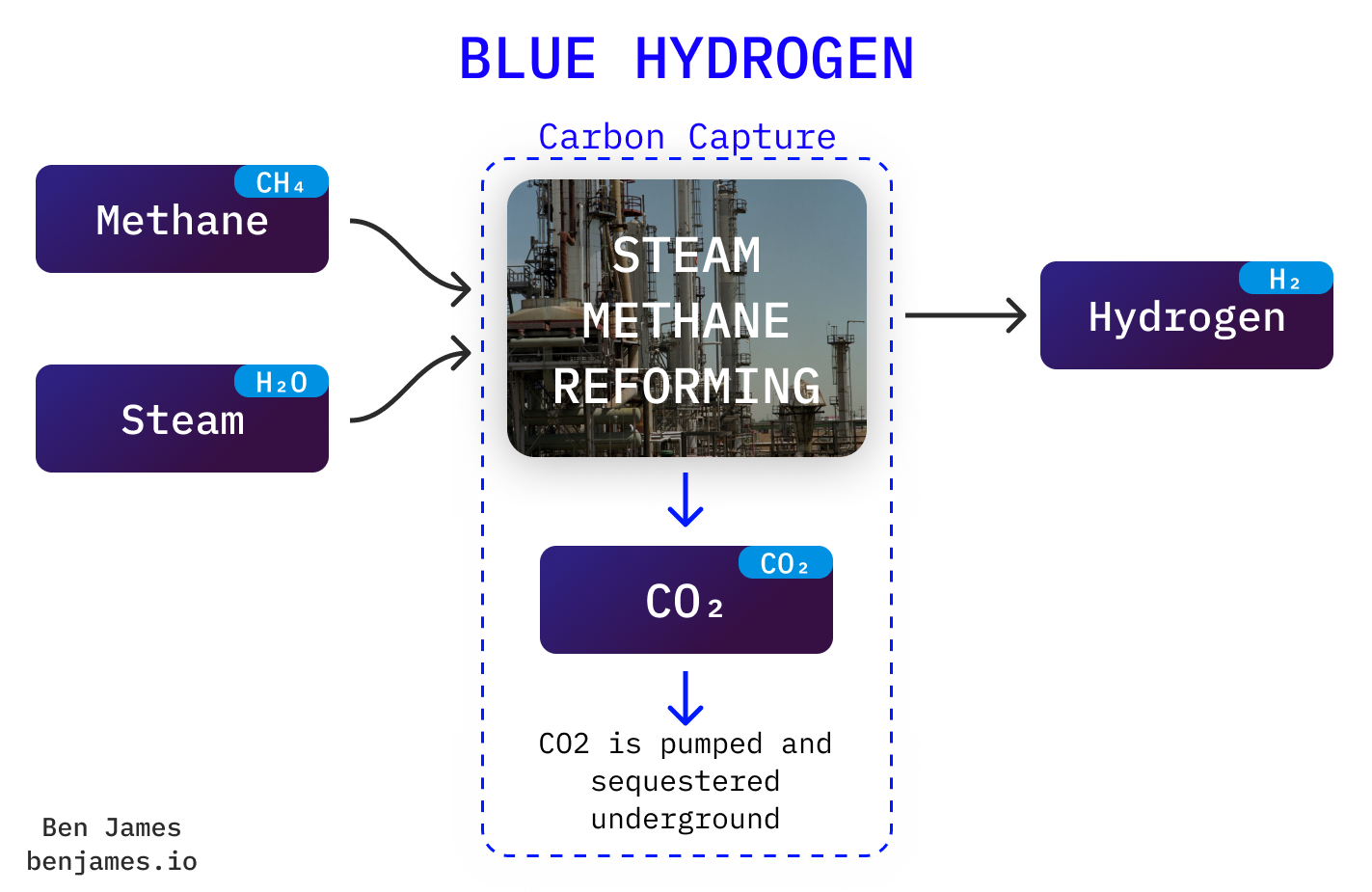
Blue hydrogen is controversial, cos carbon capture has a long history of... not working. Carbon capture tech is pretty simple, but the incentives for companies to make it work are poor. You are adding cost & energy requirement (all downside) for no financial gain.
Additionally, blue hydrogen still uses methane (natural gas) - which leaks during production and transport. These methane leaks can cause even more warming than the CO2 emitted from SMR (depending on where you get your methane).
It's easier to capture CO2 from hydrogen production than from other industrial processes, because SMR exhaust gases contain highly concentrated CO2 (>50%). The higher the CO2 concentration, the easier it is to capture carbon.
Green hydrogen
Now we're hitting the cool stuff. Green hydrogen is the most important production method to understand.
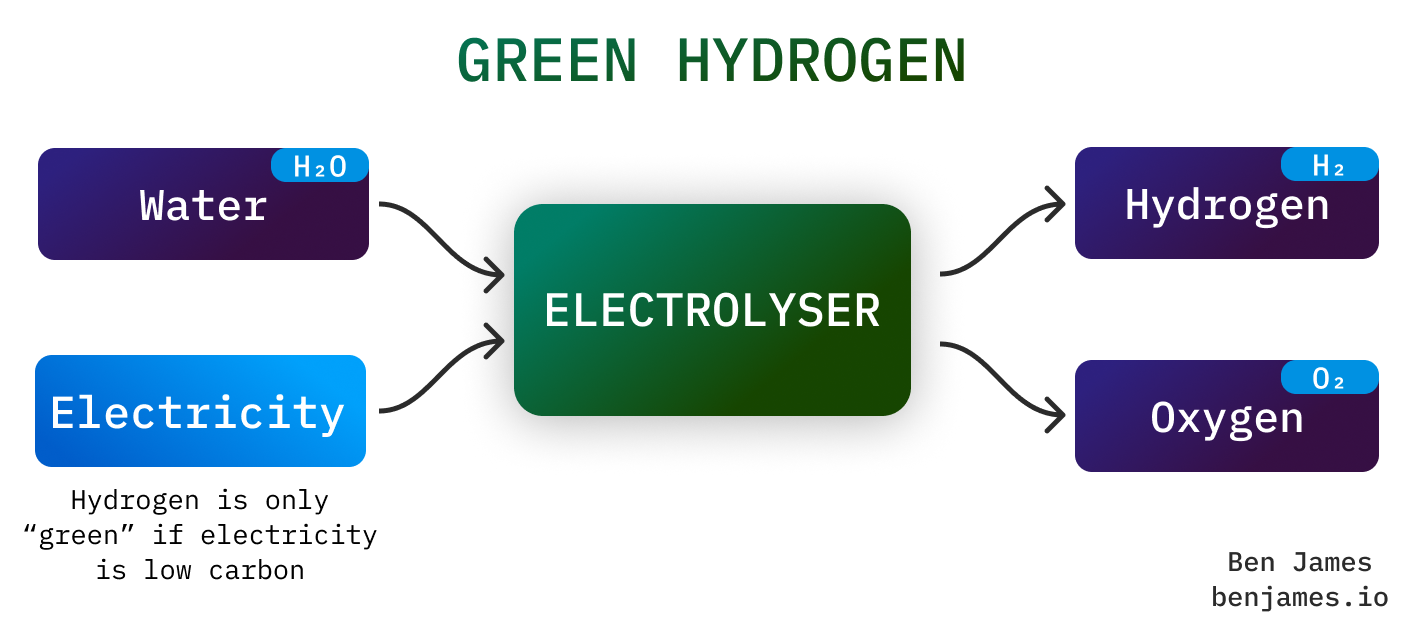
Making green hydrogen is simple: it’s just two electricity-conducting sticks in some water. Passing electricity through H2O splits it into H and O.
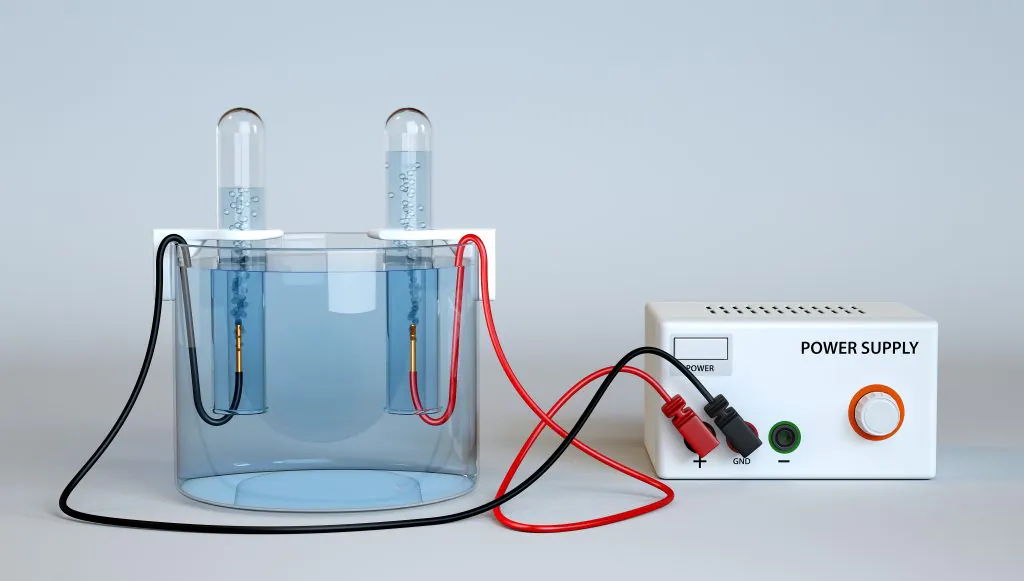
(PS - if you are a looking for a climate tech activity for a dinner or an EXTREMELY ROMANTIC DATE, make green hydrogen with a 9-volt battery, two pencils, and a glass of salty water)
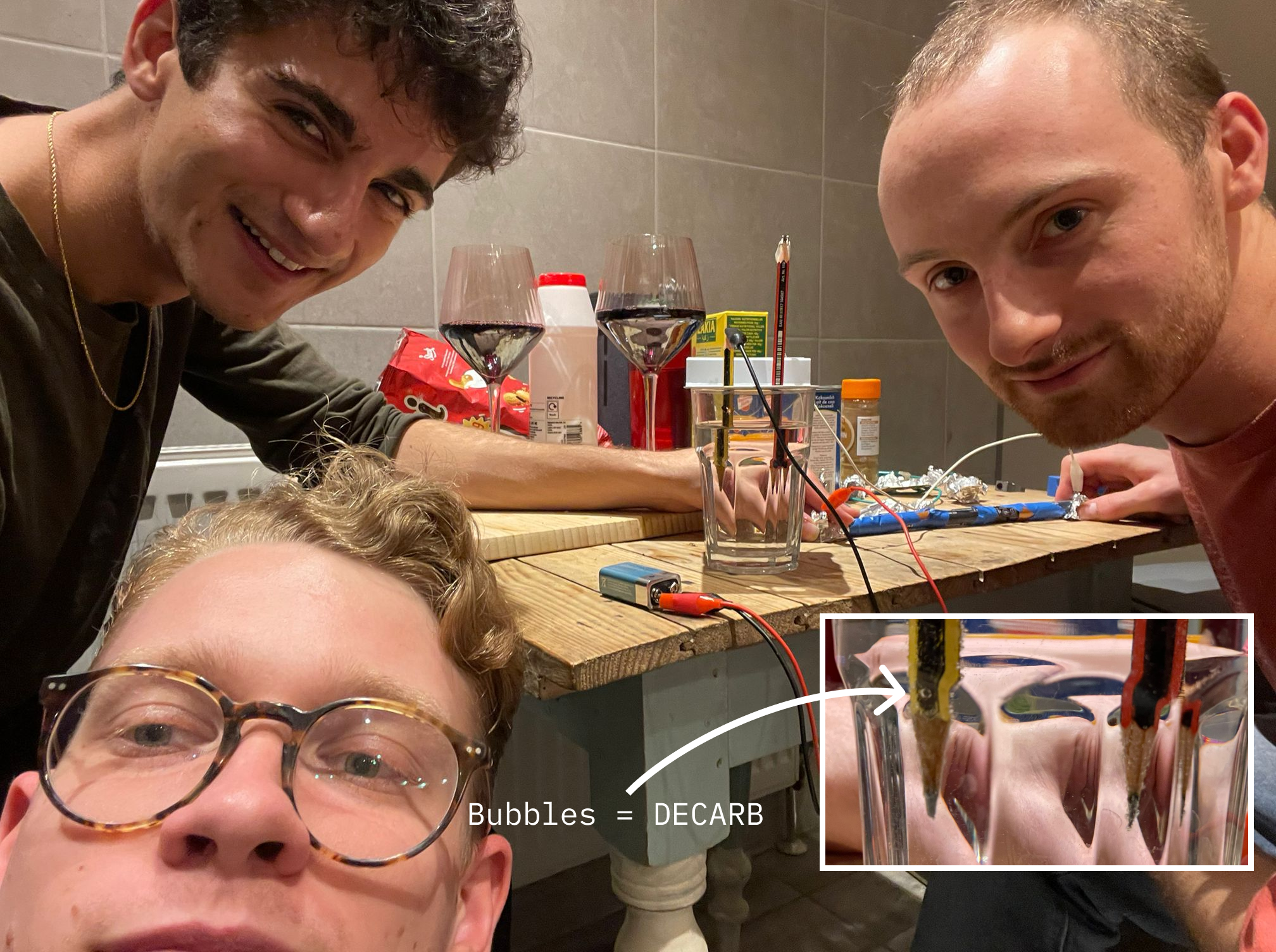
Green hydrogen uses a lot of electricity
It’s important to understand how green hydrogen is made, because it will have a huge impact on our global energy system.
The IEA predicts that by 2050, making green hydrogen will use 20% of global electricity.
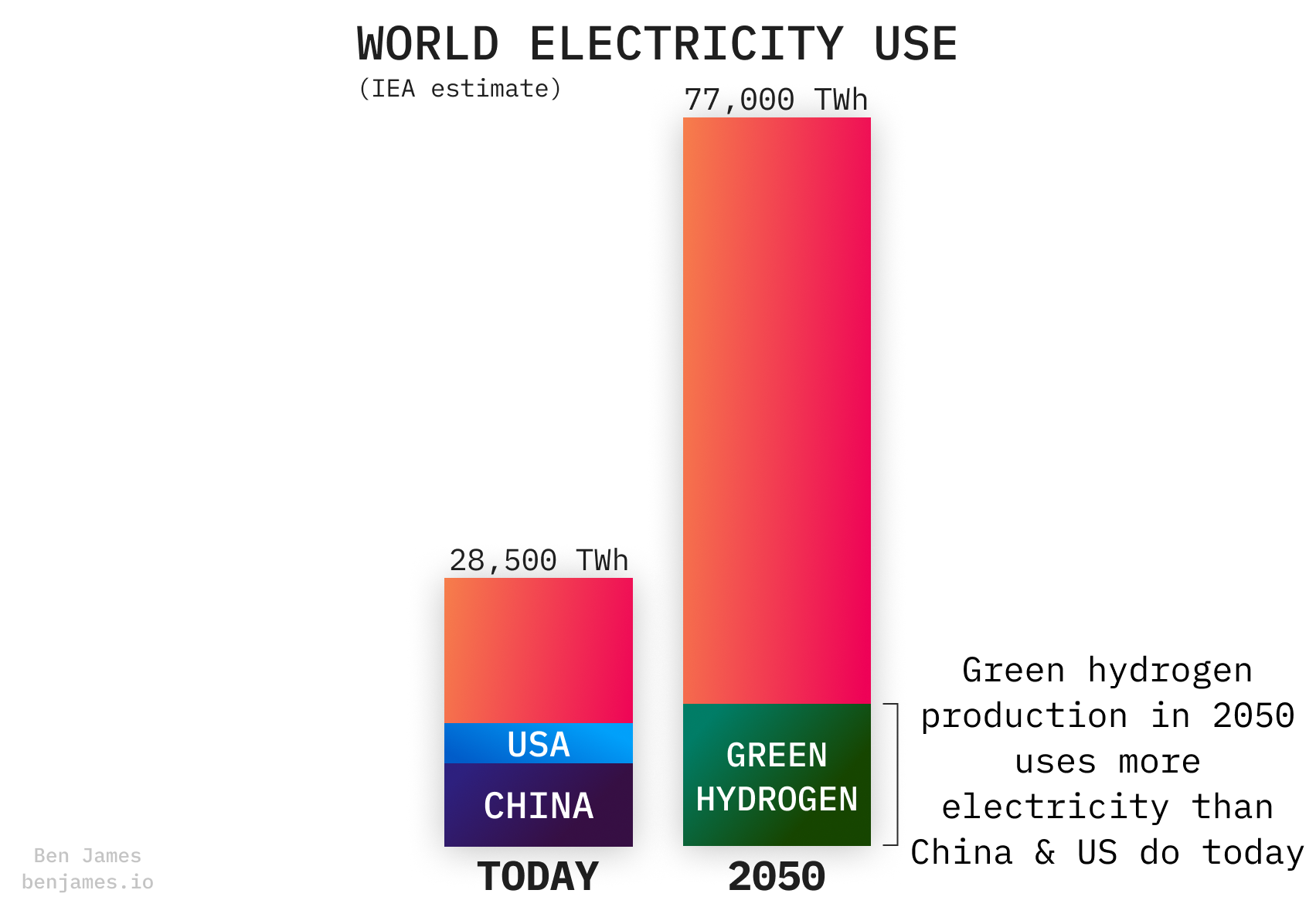
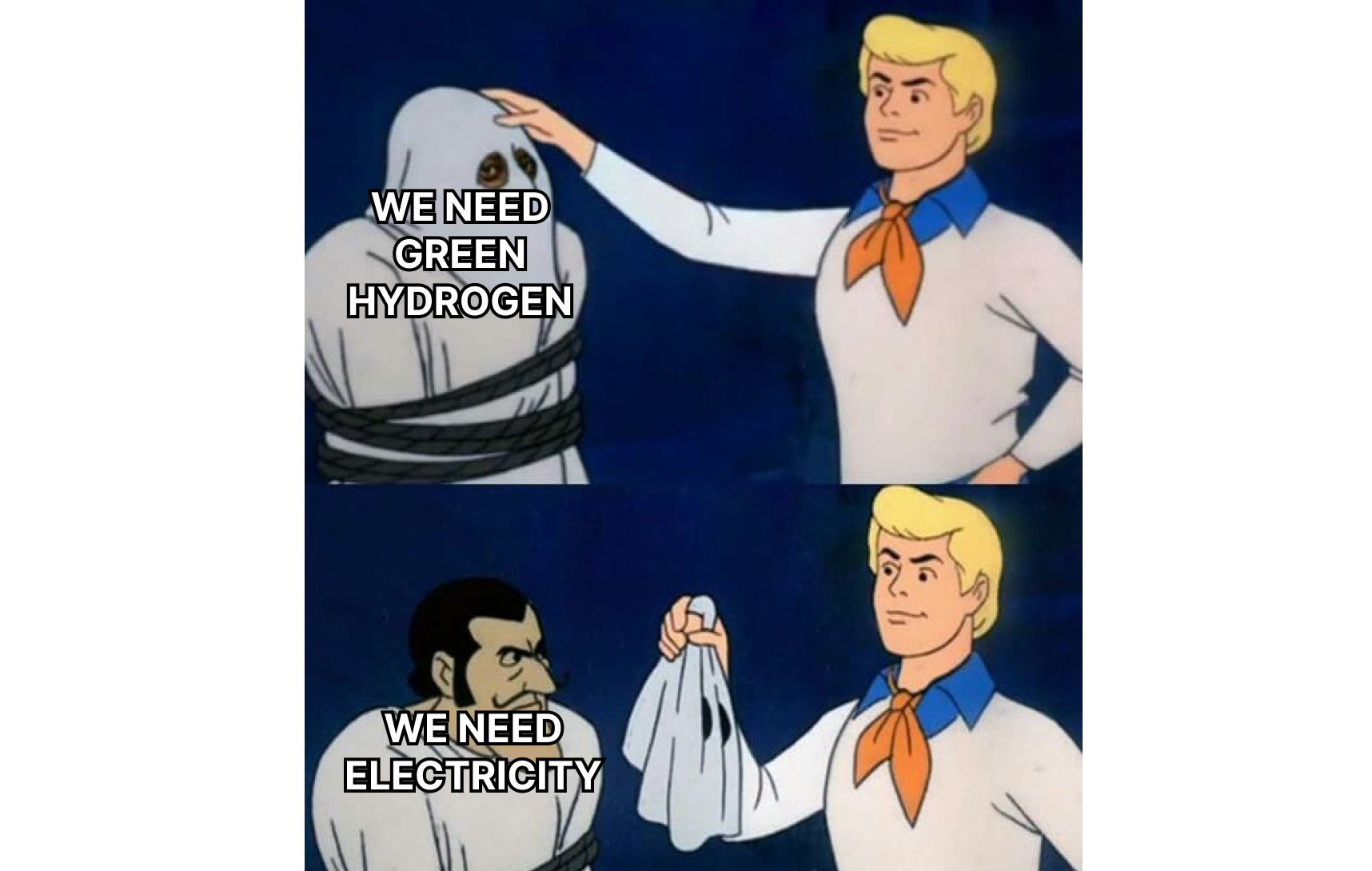
Let’s learn a bit more about the machines that will slurp up all this electricity.
Electrolysers
Splitting water to make hydrogen is electrolysis, and the machines that do this are called electrolysers.
There are three types of electrolysers. You can impress any hydrogen nerd by asking what type of electrolyser they’re using.
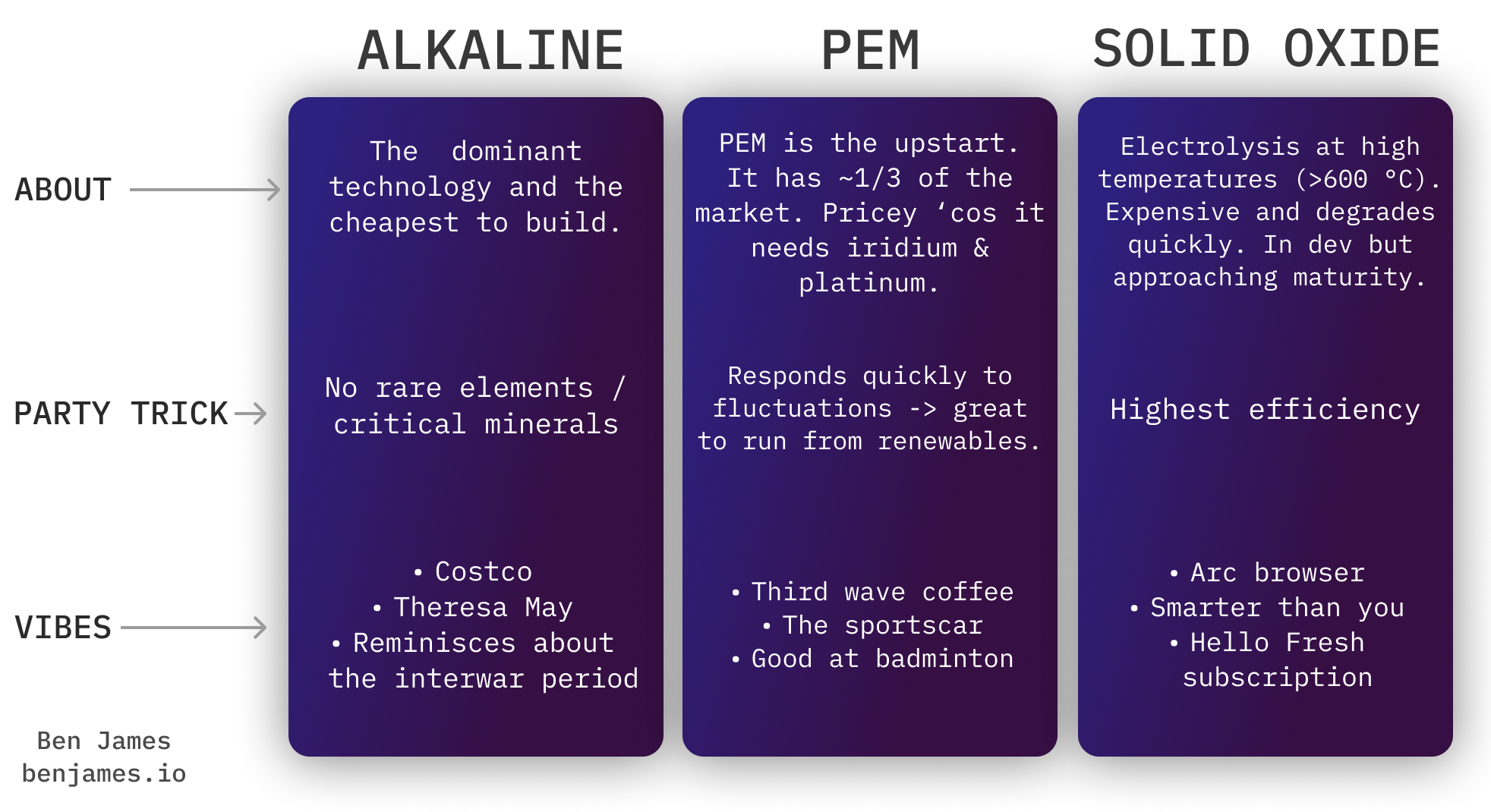
PEM is well suited to running off of renewable power, because you can temporarily overload it. It deals well with spiky electricity.
There’s also a fourth type of electrolyser called AEM - which is a cross between Alkaline and PEM. In theory, you receive the benefits of PEM (flexibility), without the high cost of the rare materials. It’s early days, but AEM is being commercialised by Enapter.
Over the past five years, we’ve installed roughly twice as much alkaline as PEM.
Unit economics of hydrogen
Let’s go through some rules of thumb for the cost and energy requirements of green hydrogen.
Heads up: people usually measure hydrogen in kilograms (kg).
Energy (kWh per kg)
To make green hydrogen, there is a minimum energy requirement. It is the minimum energy needed to split water, and it is 40 kWh per kg of hydrogen.
Of course, electrolysers are not 100% efficient, so most today achieve around 50 kWh / kg on a good day.
We can use the electricity a bit more efficiently, but the real cost reductions are in (1) finding the cheapest electricity to run the electrolyser, and (2) making the cheapest possible electrolysers.
Cost ($ per kg)
Here, we’re competing with fossil fuels.
- In Europe (where gas is expensive), grey hydrogen costs about $2.50 / kg
- In the US (where gas is cheap) grey hydrogen costs about $1.50 / kg
The dream is for green hydrogen to one day cost $1 / kg or less. At that level it would blow grey hydrogen out of the water. But is it realistic?
Firstly, let’s figure out how much the electricity for green hydrogen will cost us.
Grid electricity
Let’s initially assume that we power our electrolyser from the electricity grid.
Remember, we need 50 kWh of electricity to make a kg of hydrogen.
If each kWh costs $0.10 (roughly the price of US grid electricity), then the electricity will cost $5 per kg of hydrogen.
That’s not a good start. Even with the colossal IRA subsidy of $3 / kg for green hydrogen, we’re still far from our target price of $1 / kg. And we haven’t even spent any money to build an electrolyser yet.
Off-grid electricity
If electricity at $0.10 per kWh is too expensive, where can we find some that’s cheaper?
The answer is renewables. When the sun is shining and the wind is blowing, electricity is the cheapest it’s been in history.
We could either:
- Build dedicated solar or wind farms, just for powering electrolysers. Or,
- Use the excess energy from existing renewables, when they generate too much energy.
(That second one might sound silly - how can we have too much renewable energy? But it’s actually a big problem. In the UK we spend £billions per year turning off wind turbines).
The problem with both of these approaches is that you build an expensive electrolyser that just doesn’t get used very often - because renewables are intermittent.
The best way to get an intuitive grasp of the CAPEX/OPEX tradeoff here is to play around with a hydrogen calculator. I like Electric Hydrogen’s one.
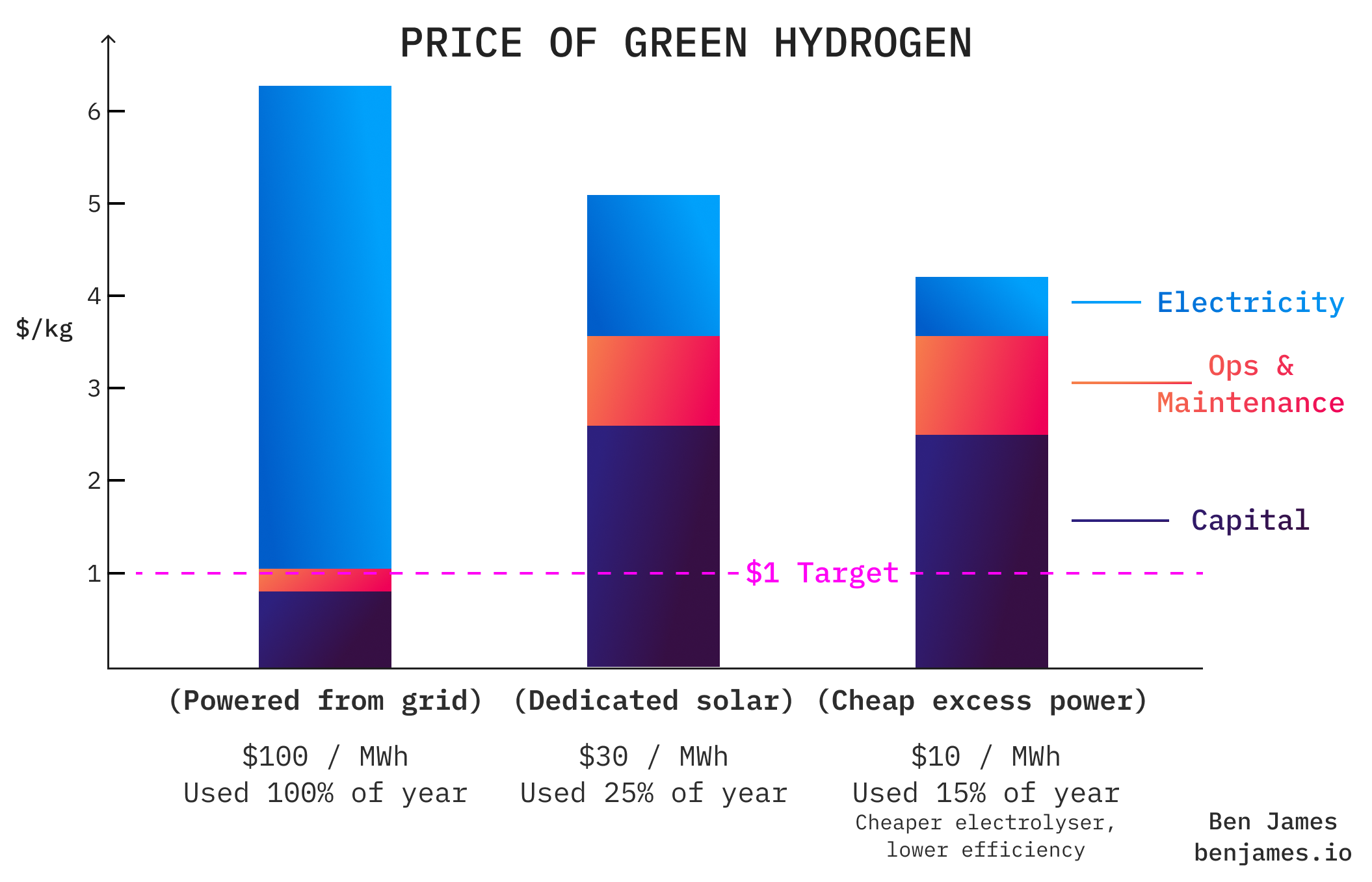
This means that the hydrogen tech we should be building is the opposite to what many assume (and what most acadamic research is focused on). It’s not about making efficient electrolysers that are cheap to run, it’s about making rudimentary ones that are cheap to build. Reducing CAPEX, not OPEX, is the key to building an electrolyser that can pay off its costs.
Transport
Hydrogen is a pain to handle. Today, most hydrogen is not transported at all. It’s used right next to where it was produced.
Hydrogen is tricksy because (1) it’s not very dense, (2) it’s a very small molecule, so it leaks a lot, and (3) hydrogen is very flammable - The Hindenburg was not cool.
You can move hydrogen by pipeline, truck, rail, or boat.
Pipeline
Sometimes, natural gas pipelines can be repurposed to carry hydrogen - but there are some hefty caveats.
Three things to consider:
- Leaks. Hydrogen is the smallest molecule in the world. It will find its way out of seals, valves and cracks that natural gas would not.
- Embrittlement. Local gas distribution pipes (made from soft steels and plastic pipes) can handle hydrogen just fine. But putting hydrogen through large national gas pipelines - made from hard steels - can “embrittle” (corrode and crack) the steel.
- Compression. To deliver the same amount of energy using hydrogen as with natural gas, you must use 3x the energy compressing it (h/t Paul Martin). That’s why today we pump around natural gas instead, and turn it into grey hydrogen where required.
Since hydrogen takes up 3x more space than natural gas (for the same energy), a blend of 10% volume only replaces 3% of the energy content. You have to pipe more of the blended mixture to compensate for the lower density.
Truck
Hydrogen as a gas at room temperature takes up a lot of space. Roughly 3x more space than natural gas, and 300x more than diesel.
So moving it in its uncompressed form isn’t an option: we have to squish it.
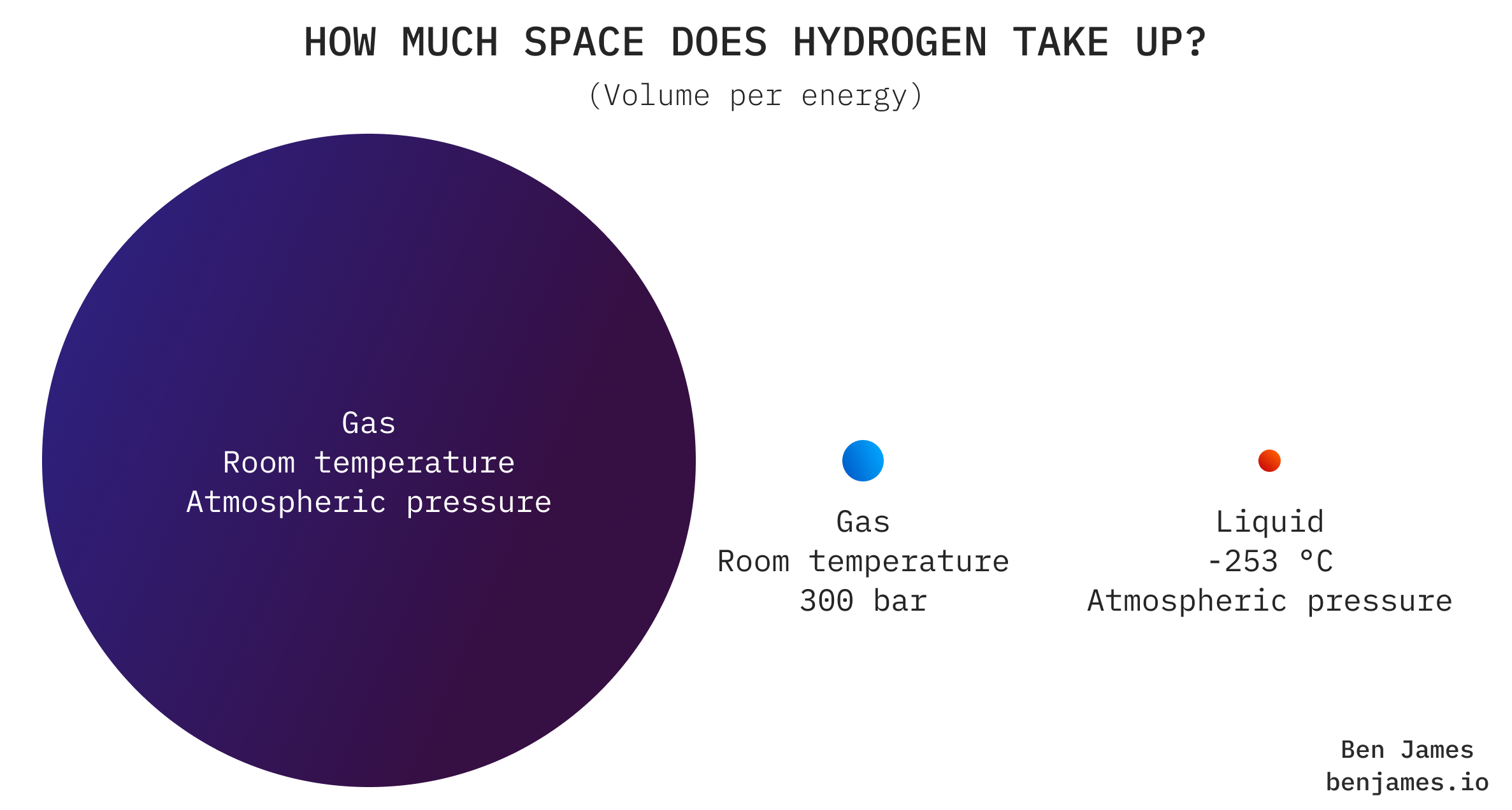
To put hydrogen on the road, you can either: (A) cool it a lot and transport it as a liquid in a tanker, or (B) pressurise it a lot and transport it as a gas in a tube trailer.
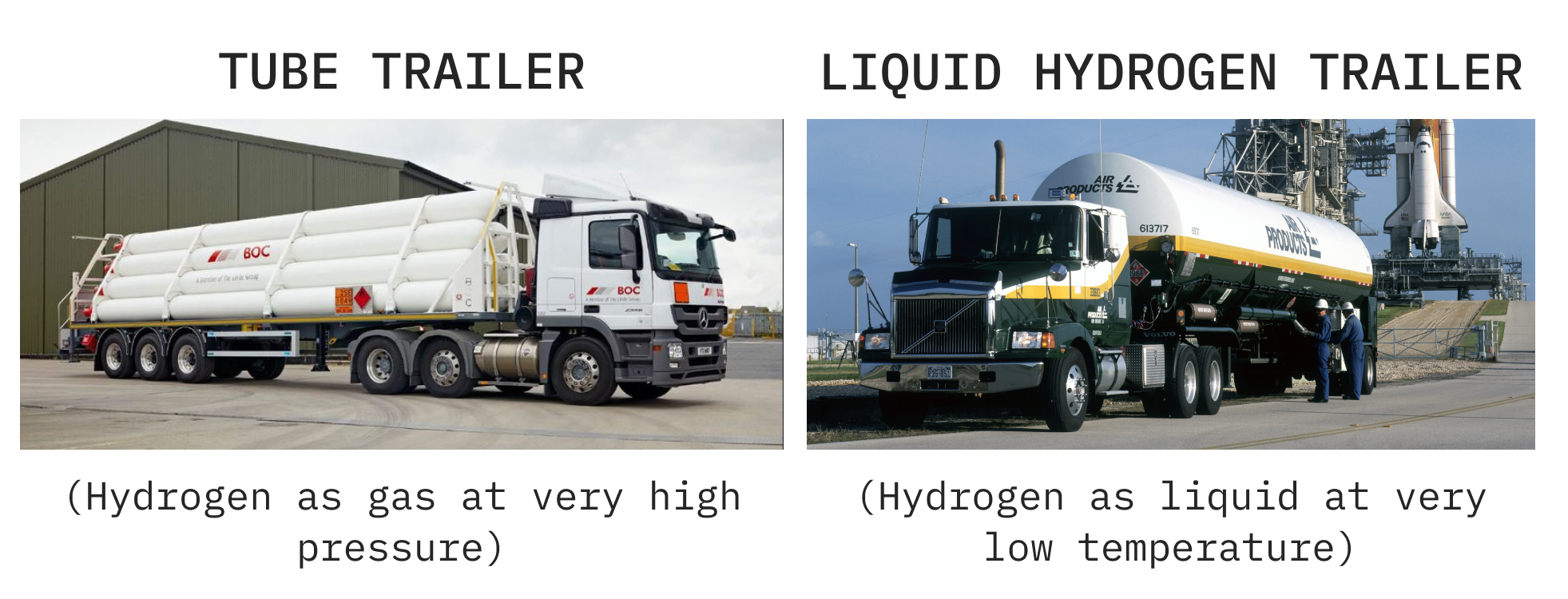
Both of these options are a bit pants. Liquifying hydrogen uses up about 30% of its energy, and hydrogen as a gas just isn’t very dense. You’d need >10 tube trailers to transport the same energy as a diesel tanker truck.
Ship
Fun fact: there is one hydrogen tanker in the world, and it is the Suiso Frontier - made in 2019.
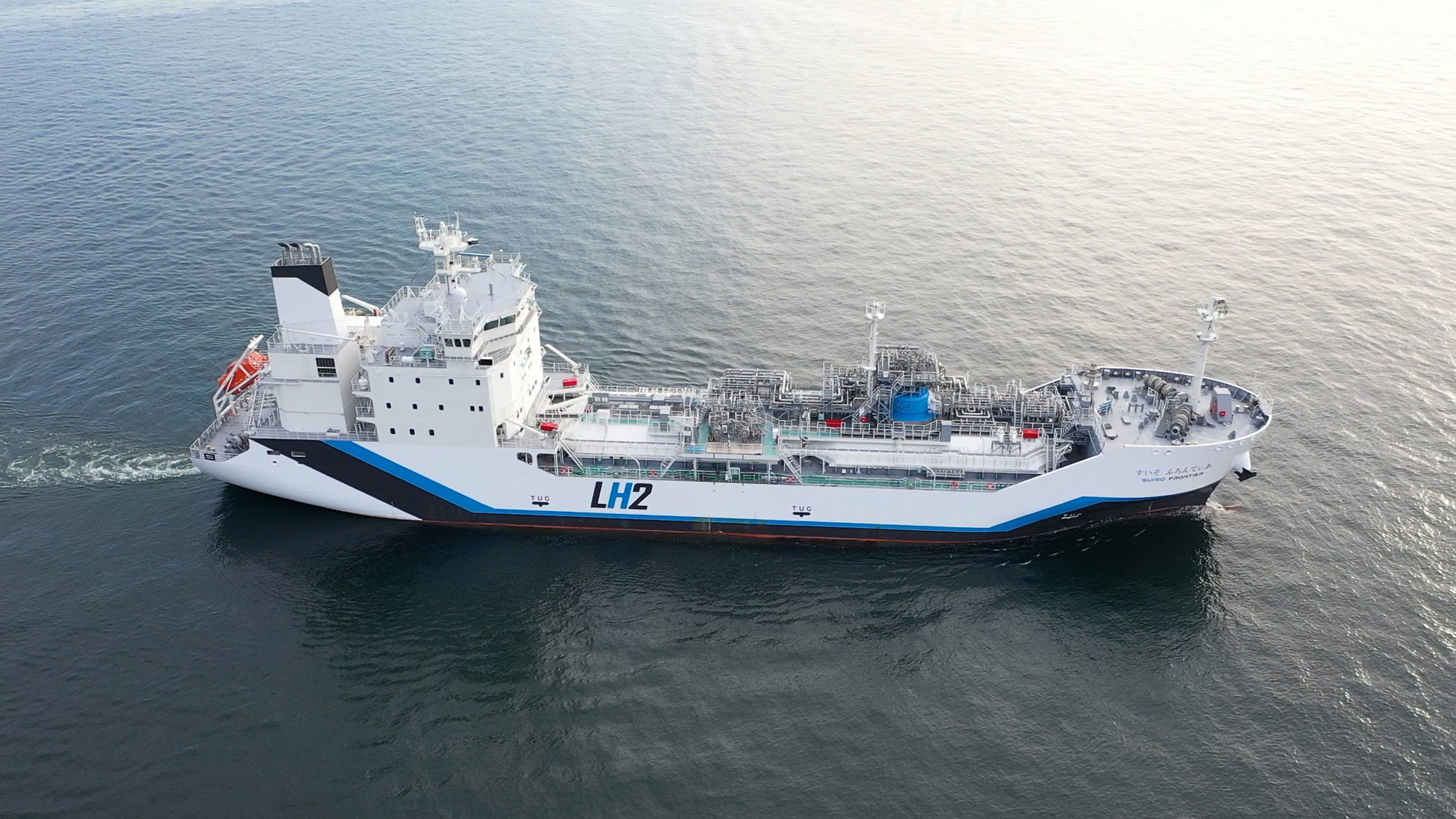
We liquefy hydrogen to ship it, and so we encounter the same 30% loss from liquefying it - plus around 0.2-1% of the hydrogen will “boil off” for every day of the voyage.
Shipping pure hydrogen is rubbish. A more attractive way to ship hydrogen is in the form of ammonia. People sometimes refer to ammonia as a hydrogen carrier. This is pretty interesting, and we’ll cover it in part two of this series, which is all about ammonia!
Storage
Lastly, we have storage.
We can store hydrogen as a dense liquid for a short time, but because we have to keep it at -253°C, it would be too energy intensive to do this for long periods.
That means we have to store it as a gas. Storing it in big gas tanks is tricky, because (1) they'd have to be huge (2) you're storing a a very flammable gas, and (3) the hydrogen will just escape. Yep, hydrogen will literally just diffuse through a steel wall, which is sooo annoying. As the smallest atom, it's hard for other atoms to keep it in check.
Luckily some geographies are blessed with the ability to store hydrogen underground. There are three main places we could store it: gas fields, aquifers, and salt caverns. These are the same places that we store natural gas. If you want to learn more, the wikipedia page on geological natural gas storage is a great place to start.
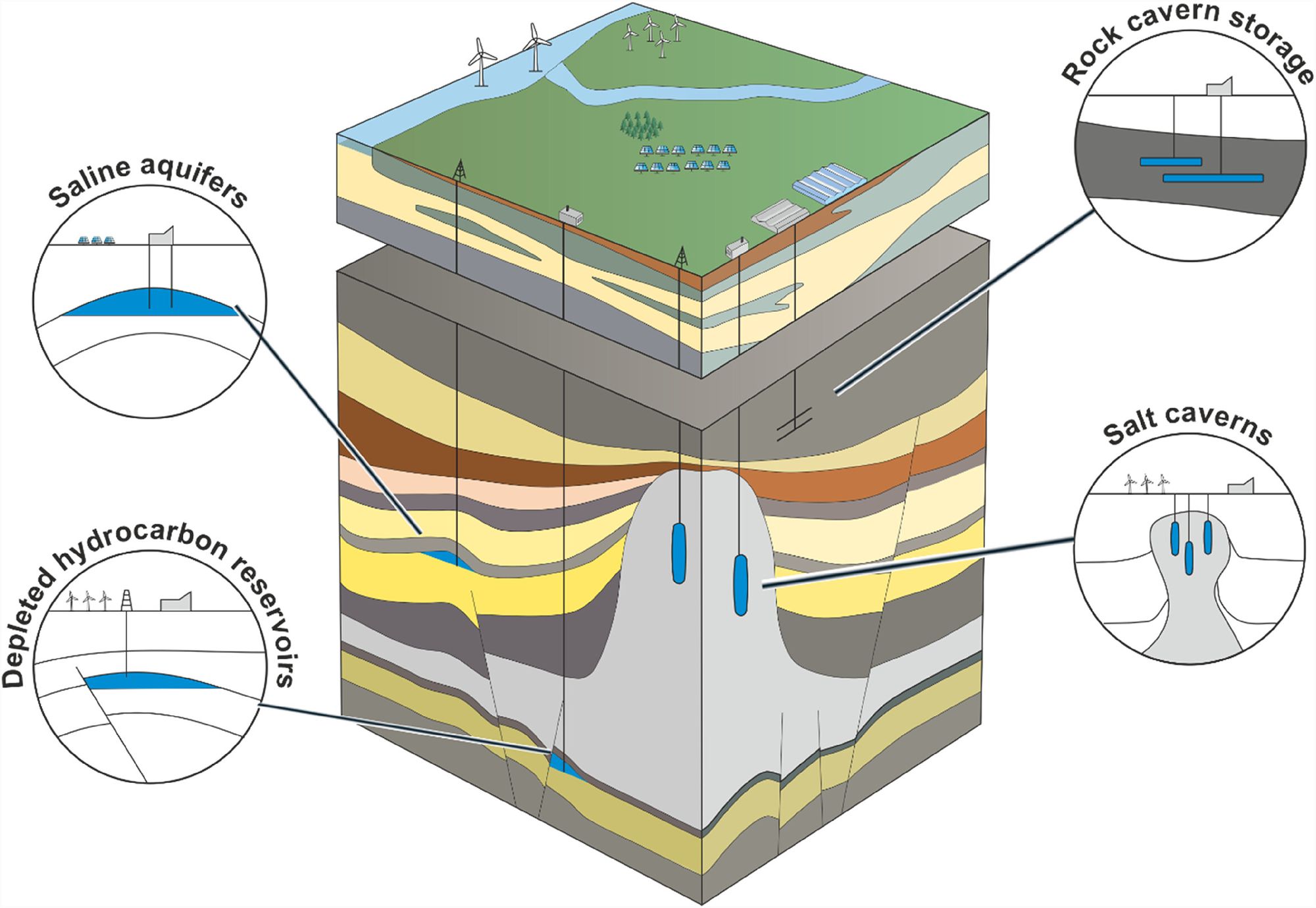
Conclusion
We will need a lot of green hydrogen - even if it's not as much as the natural gas industry wishes.
That means we'll need an eye-popping amount of electricity to make it. This simple fact produces some of the biggest costs & headaches in industrial decarb. If you want to make a clean steel plant that uses green hydrogen, the easy part is building the green steel plant. The hard part is sourcing the green hydrogen and necessary TWhs of electricity.
Huge thanks to Gniewomir Flis for giving his thoughts on this piece. Opinions and mistakes are all mine.
Next up: ammonia.
This was #1 in my series on climate molecules. Keep reading here!