Energy Fundamentals of Carbon Capture
In this post, I cover carbon capture (removing CO2 from the chimneys of power stations and industrial plants).
In the next post, I cover engineered carbon removal (removing CO2 directly from the air).
Carbon capture and carbon removal can seem like dense topics that only a scientist can understand. But they’re actually pretty simple processes.
Here, I’ve distilled the energy requirements of CO2 capture systems to their fundamentals, whilst still including the details that are interesting.
Why energy requirements? That sounds boring.
(1) It’s the best way to cut through a complex topic
Thinking in terms of the energy per tonne of CO2 can give you most of the understanding for little of the effort. Even better, many of these numbers are physical laws, so won’t change in future.
(2) It’s the most important bottleneck
When engineering systems to deal with CO2, energy consumption is king.
Let’s take the example of Direct Air Capture.
- Current processes use a bit more than 2000 kWh of energy to capture one tonne of CO2.
- This means that capturing one year of global CO2e emissions would require ~120,000 TWh of energy.
- 120,000 TWh is about the same amount of energy that the world uses per year. So we’d have to double the world’s energy supply just to power our giant hoover. [1] [2]
No-one is proposing that we capture all of our emissions with Direct Air Capture. But energy use is clearly important.
In this series I’ll break down (A) where these huge energy requirements come from, and (B) what is unavoidable physics, and what is fertile ground for improvement. You won’t need a technical background to understand this post, you’ll just need to know that energy is measured in kilowatt-hours (kWh).
The basics
We need to quickly cover some basics before we dive in. I've put these in dropdowns in case you already know them.
The difference between carbon capture and removal
The difference is very important.
Carbon capture refers to the removal of CO2 from point sources - the chimneys of industrial plants and power stations. This post is about carbon capture.
- When we sequester the captured CO2 underground, we call it Carbon Capture and Storage (CCS).
- When we use the CO2 (eg to make chemicals or fuels, or to extract more oil 😲), we call it Carbon Capture and Utilisation (CCU).
- CCUS (Carbon Capture, Utilisation and Storage) encompasses both and refers to the whole industry.
Carbon removal refers to the removal of CO2 from the atmosphere. Sometimes it’s called Carbon Dioxide Removal, or CDR. We can do this with nature or technology. When we do it with technology, it’s called Direct Air Capture (DAC). Post 2 in this series is about DAC.
Yo, isn’t carbon capture just a distraction from real emissions reduction?
In >90% of cases, yes it is. We should decarbonise everything that we can without using carbon capture. But there are still things that we don’t know how to decarbonise without it, such as cement plants, or long-haul aviation (the carbon in clean aviation fuels comes from carbon capture).
If we are serious about the world reaching net zero emissions, then it is obvious that carbon capture will play a small role. It’s therefore important to understand what’s possible with carbon capture, so that we know where to use it or avoid it.
Energy visualised
Let’s get started. This figure summarises what we’re about to learn. How much energy does it take to capture a tonne of CO2 via different methods?
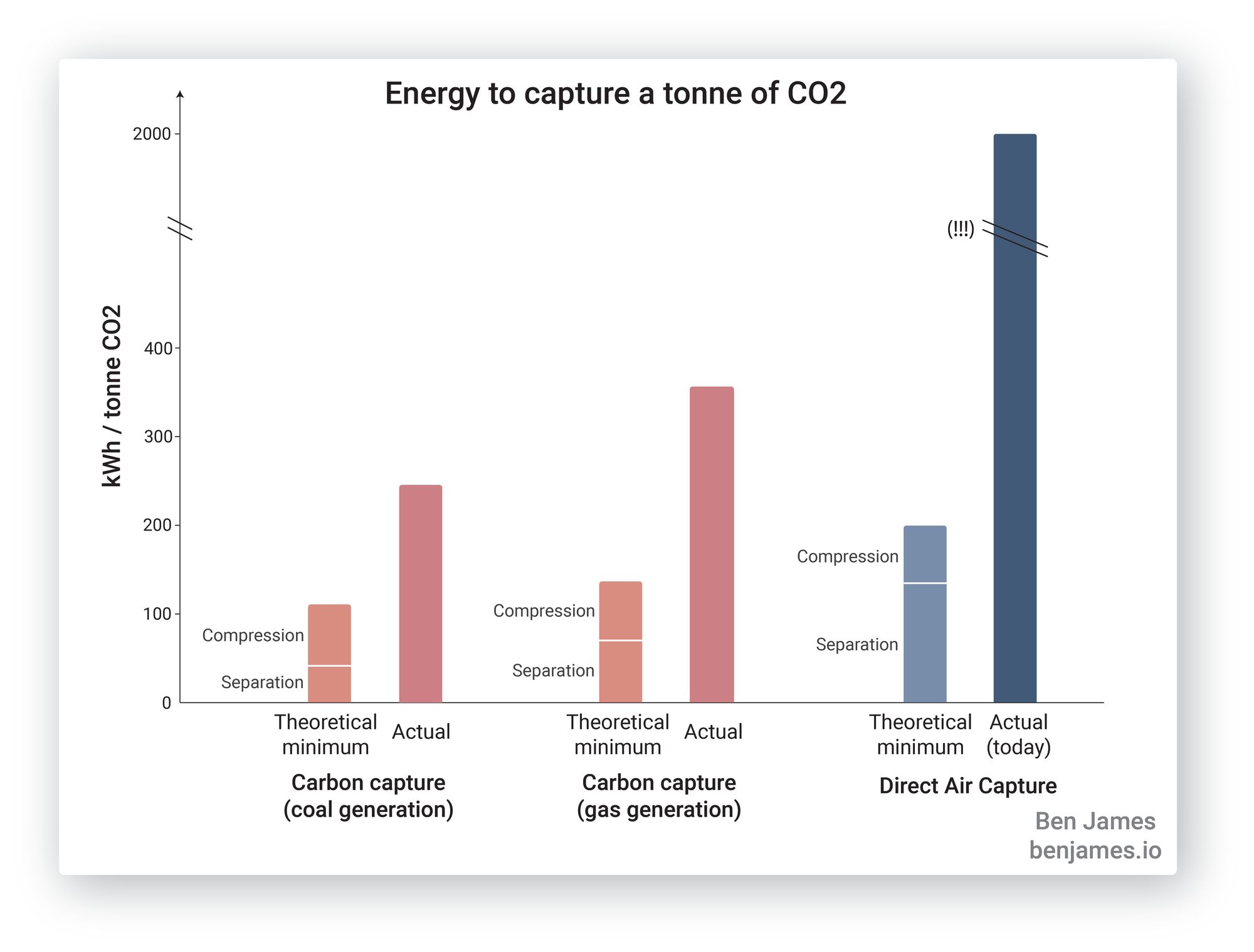
As you can see, point-source carbon capture takes a lot less energy than removing CO2 directly from the atmosphere. Let’s learn about it.
Carbon capture
The oil and gas industry developed technology for removing CO2 from gas streams many decades ago (for natural gas processing). The dominant technology here (“amine scrubbing”) hasn’t fundamentally changed in a long time. I’ll explain how this process works later in the post.
Note that this is very different from Direct Air Capture technology, which has evolved a lot in the past decade, and is the subject of considerable research & innovation. There are several technologies for point source carbon capture, but we’re only going to talk about the big daddy, which is post-combustion capture. Post-combustion means that you use your industrial plant as normal, and plop your capture equipment on the chimney to “filter” the exhaust gases. Other capture methods involve expensive modifications to how fuel is burned inside the plant itself. They are less proven and generally more expensive to retrofit.
Give me the numbers
We’re going to walk through the energy needed for carbon capture by looking at three important figures.
#1 - separation of CO2 (theoretical minimum)
Separating CO2 out of a mixed blend of gases requires some energy. In fact, there is a fundamental physical limit on the minimum energy required to do this.
For a standard coal power plant, the minimum energy requirement to separate CO2 from the exhaust gas is 43 kWh / tonne CO2 captured. [3]
For context: an average Brit takes about 28 days to emit 1 tonne of CO2, and 12 days to use 43 kWh of household electricity [10]
This minimum energy depends on a few important things. The most important factor is how much of the exhaust gas is CO2 to start with. For our coal plant calculation above, we assume that we’re capturing from an exhaust gas with a CO2 concentration of 11%, and capturing 90% of the CO2.
What about a power plant that burns natural gas instead of coal? It turns out that the minimum energy for separation is higher. Natural gas is a cleaner fuel, so the exhaust gas of the power plant has a lower CO2 concentration of about ~4%. This means that the needle that we’re trying to find in our haystack just got smaller - so we’ll need more energy.
For a natural gas power plant (combined cycle), the minimum energy requirement for CO2 separation is 70 kWh / tonne CO2 captured. [4]
#2: compression of CO2 (theoretical minimum)
Now that we’ve separated out our CO2, we have pure CO2 gas. But to transport the CO2 through a pipeline and/or pump it underground, we’ll usually need to turn it into a liquid. So we need to compress it.
Our theoretical minimum for compressing the CO2 (to a pressure of 110 bar) takes about 61 kWh / tonne CO2. This is the same for coal or natural-gas-based power. [5]
#3: Real life
Our theoretical coal plant capture system should consume 43 + 61 = 104 kWh per tonne of CO2.So how do we do in real life? It’s actually hard to tell, since commercial systems don’t like to publish their operating numbers. But after some digging [6], I’m confident that 250 kWh per tonne is a solid average for real world coal plants. For (combined cycle) gas power plants, you can expect 350 kWh per tonne of CO2. [7]
Here are the numbers in summary:
Is this a lot of energy?
A typical coal plant might produce 1200 kWh of electricity for every tonne of CO2 it emits. [8]. So a significant proportion of the energy produced by the power plant will be needed to power the CCS equipment. This is referred to as the “energy penalty”.
Not all of the 250 kWh will come out of the 1200 kWh electrical output of the plant, since some waste heat from the plant can be used (more on this below). Nonetheless, adding carbon capture to a power plant significantly reduces the amount of electricity it can sell to the grid.
What is all this energy actually used for?
To examine this, we have to peek under the hood of the carbon capture process.
Here’s a simplified diagram of the typical post-combustion capture process.
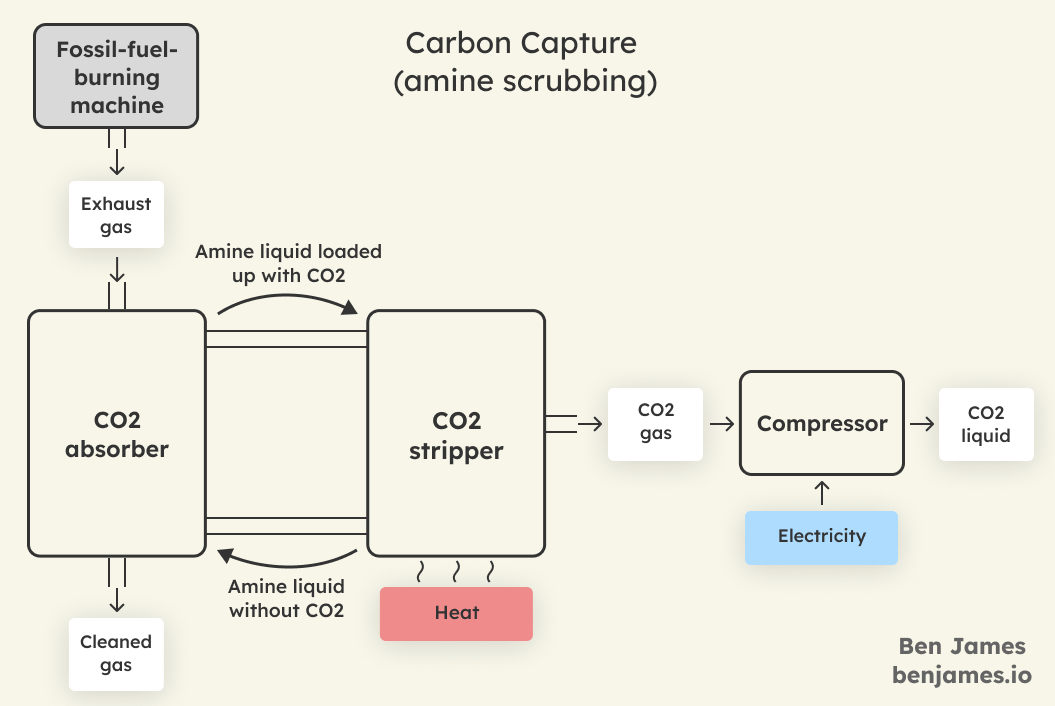
This standard process uses amines (a type of chemical) to remove CO2.
- First, the exhaust gas is passed through the CO2 absorber, where the CO2 in the gas is absorbed by the amine liquid.
- Next, the amine liquid is pumped into the CO2 stripper, where the liquid is heated up with steam. This causes the amine to let go of the CO2. This process is called regeneration.
- The amine liquid can now go back to the absorber and start again. The CO2 gas is now separated and can be compressed.
The regeneration process dominates the energy consumption - we need to supply a lot of heat to strip the CO2 from the amine.
In a typical coal plant, the energy breakdown is:
- 60% for steam needed in the stripper
- 35% for electricity to run the compressor
- 5% for running pumps and misc. equipment
[9]
For power plants, waste steam/heat is usually tapped off to use in the stripper. Using it will still reduce the energy output of the plant, but it’s not a 1:1 reduction of the electrical output power.
Carbon capture isn’t just for power plants
In this post we’ve looked at carbon capture on power plants, since they are a frequently discussed target. But carbon capture can be used on other industrial processes too.
An important factor to understand is that capturing carbon from different industrial processes is a dramatically different experience. Ie, the ease of carbon capture varies significantly between different industries. The easiest processes are those with a high concentration of CO2 in their exhaust, a high pressure of exhaust, or high availability of waste heat. Here are some cost estimates from the IEA.
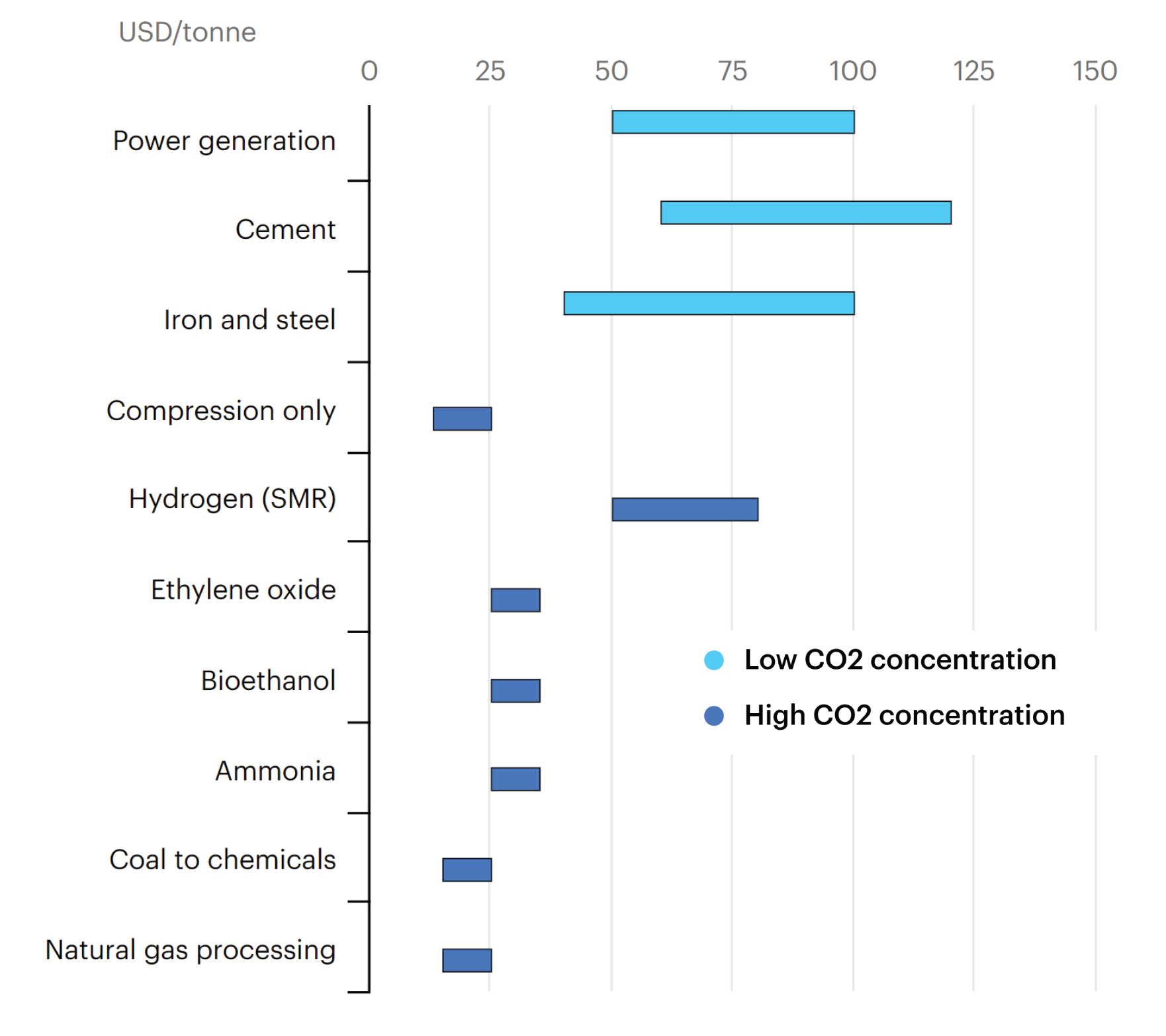
Onwards..?
Will carbon capture get much closer to theoretical minimums? Probably not. Incentives have been good for oil and gas companies to improve this technology for a while now, and it has become standard chemical engineering. There are improvements to be made in the cost, stability and lifetime of the (expensive) amine chemicals used, but these are incremental progress, not breakthroughs.
Part 2
This post covered carbon capture, and was part 1 of 2. Part 2 covers carbon removal - a space with a lot more change, competition, and innovation.
👉 👉 Read part two here! 👈👈
I’m grateful to Art (who writes a killer climate tech blog) for reviewing and offering his thoughts.
Sources and footnotes are linked here.
Who's Ben James?
I spend my time deconstructing climate tech, and sometimes write down my thoughts on this blog. I’ve previously worked at World Fund, Octopus Energy, and the IPCC.
Sometimes I run training sessions for investors who want to study climate technologies in depth. Email ben at benjames.io.
Other writing
If you enjoyed reading this, you might enjoy some of my other posts: